Understanding Safe Operating Procedures (SOPs):
What They Are and Why They Matter.
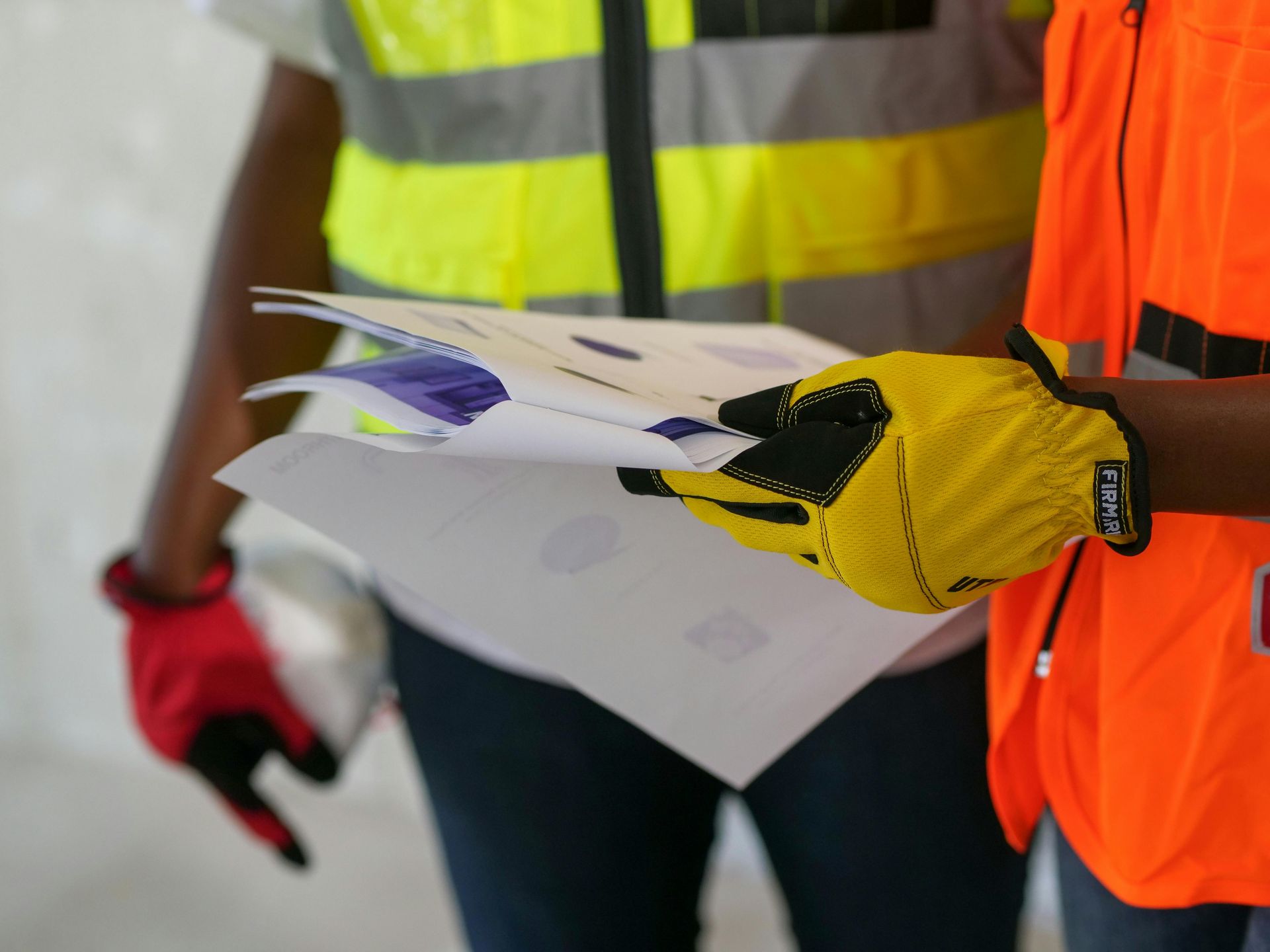
In the world of workplace safety, Safe Operating Procedures (SOPs) are not just helpful tools – they are essential components for protecting workers, complying with the law, and maintaining efficient operations. Every task, machine, and process carries its own risks, and SOPs are there to manage those risks systematically.
In the United Kingdom, having clear and effective SOPs is not simply good practice — it is often a legal requirement under key health and safety legislation, including the Health and Safety at Work etc. Act 1974 and associated regulations.
Let’s explore what SOPs are, why they are so important, and how they fit into the UK’s health and safety landscape.
What is a Safe Operating Procedure (SOP)?
A Safe Operating Procedure (SOP) is a detailed, written set of instructions designed to guide workers safely through the steps of a specific task, piece of equipment, or work process.
A good SOP typically includes:
- The task description (what needs to be done)
- The equipment or tools required
- Potential hazards involved
- Step-by-step instructions to perform the task safely
- Control measures (e.g., PPE requirements, safety checks)
- Emergency procedures in case something goes wrong
- Reference to relevant risk assessments and legislation
SOPs should be clear, concise, and accessible to anyone undertaking the task, whether they are seasoned professionals or new employees.
Why Are SOPs Important?
SOPs serve several vital functions:
1. Worker Safety
By providing clear, standardised instructions, SOPs help ensure that tasks are carried out safely and consistently, reducing the likelihood of accidents, injuries, and near misses.
2. Legal Compliance
Under the Health and Safety at Work etc. Act 1974, employers have a duty to ensure, so far as reasonably practicable, the health, safety, and welfare of employees and others who may be affected by their work activities. SOPs form part of the evidence that an employer has taken reasonable steps to control risks.
Other important regulations where SOPs support compliance include:
- The Management of Health and Safety at Work Regulations 1999 (risk assessments and training)
- The Provision and Use of Work Equipment Regulations 1998 (PUWER) (safe use of equipment)
- The Control of Substances Hazardous to Health Regulations 2002 (COSHH) (safe handling of chemicals)
3. Training and Supervision
SOPs are invaluable for onboarding new staff and for ongoing refresher training. They provide a baseline standard for how tasks should be done safely and correctly.
4. Consistency and Quality
Standardised procedures mean that work is carried out uniformly, ensuring consistent quality and efficiency across operations.
5. Incident Prevention and Investigation
In the event of an incident, a properly implemented SOP can demonstrate that correct procedures were in place. Conversely, if an SOP was not followed or missing, it may highlight where improvements are needed.
SOPs and UK Health and Safety Law: How They Fit Together
The UK’s health and safety legal framework is built around the principle of risk management — identifying hazards, assessing risks, and controlling them effectively. SOPs are a practical extension of this philosophy.
Key links to regulations include:
Regulation
Connection to SOPs
Health and Safety at Work etc. Act 1974
General duty of care to employees and others – SOPs are a means of discharging this duty.
Management of Health and Safety at Work Regulations 1999
Requires risk assessments and implementation of preventive and protective measures, often achieved through SOPs.
PUWER 1998
Demands that work equipment is used safely, and SOPs are part of the required information, instruction, and training.
COSHH 2002
Safe handling of hazardous substances often requires task-specific SOPs outlining control measures.
Employers who fail to implement or enforce safe procedures can face enforcement action by the Health and Safety Executive (HSE), including improvement notices, prohibition notices, or even prosecution.
Final Thoughts
Safe Operating Procedures are not merely pieces of paperwork gathering dust in a folder. They are living documents that protect people, ensure legal compliance, and promote operational excellence.
For SOPs to be effective, they must:
- Be specific to the task and environment
- Be kept up to date with any changes
- Be communicated clearly to all relevant personnel
- Be regularly reviewed and improved where necessary
In short: SOPs save lives, protect businesses, and demonstrate commitment to a culture of safety.